ABOUT US
ARCUS Co. is internationally recognized center of competence in military engineering. It specializes in development, production and supply of the following defence products:
- Ammunition: Grenades for Grenade Launchers, Medium Caliber Ammunition, Mortar Bombs
- Fuzes: for Artillery and Tank ammunition, Mortar Bombs and Air Bombs
- Small Arms: Pistols and Revolvers
- Grenade Launchers and Mortars
ARCUS Co. employs approximately 2 900 persons, 120 engineers work on Research and Development projects. The Company is fully licensed for manufacture, trade and export of defence-related products in accordance with the Bulgarian Law and Internationally adopted regulations.
ARCUS Co. has business relations with companies, organizations and individuals from more than 75 countries worldwide. The Company policy is pointed at establishing of long-term partnership based on mutual confidence and satisfied standards.
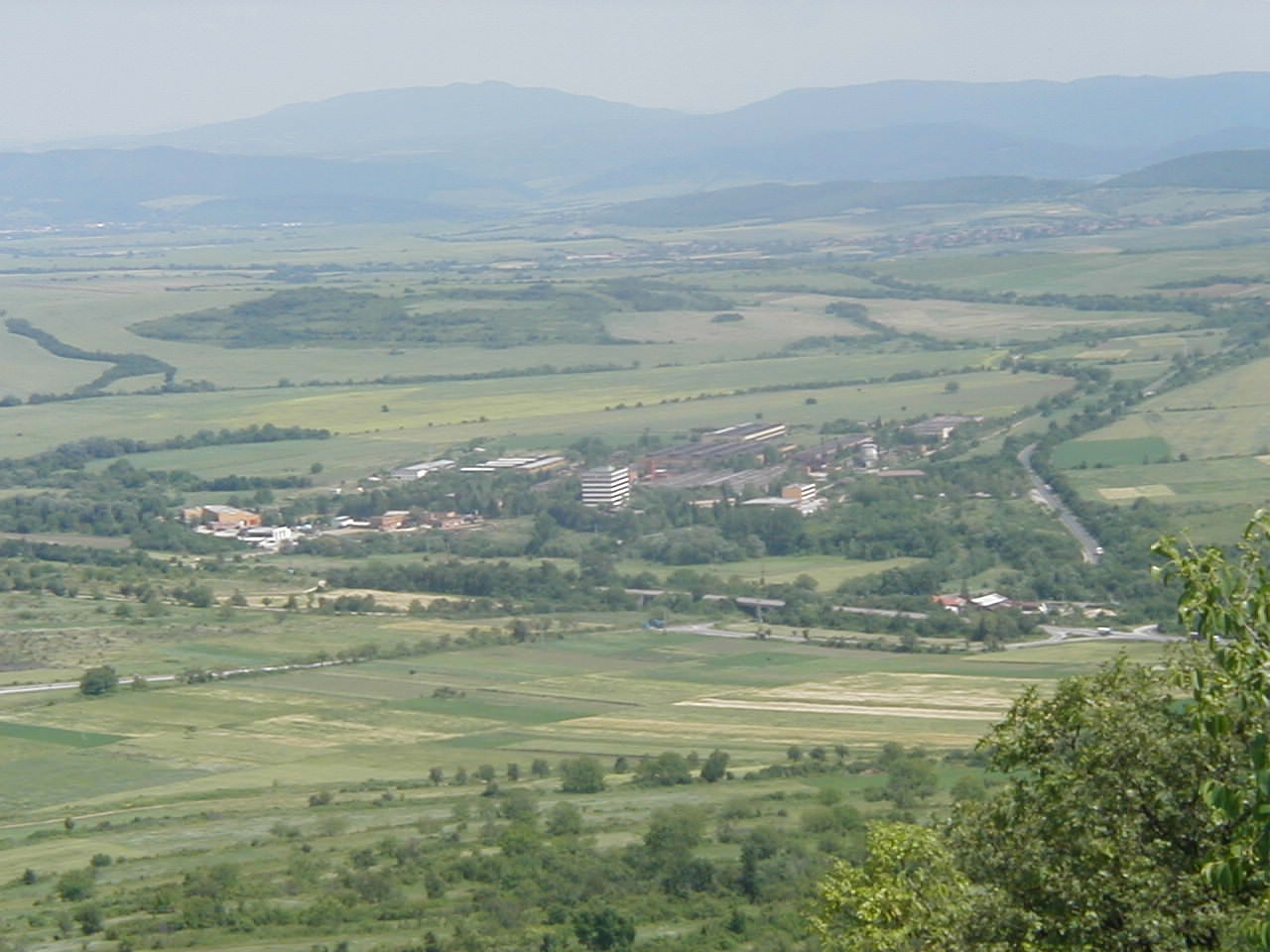
HISTORY & EXPERIENCE
The Company was founded in 1965 as a mechanical engineering plant for production of fuzes. Through the years it expanded its product range to include ammunition, small arms and close support weapons Now the Company has 40 years of tradition in research, development and manufacturing of defence-related products.
QUALITY AND CERTIFICATES
The Company’s performance is focused on quality. The quality of our products is based on years of research and experience, highly specialized workforce, advanced equipment and testing facilities.
The Company is certified for compliance with ISO 9001 ; ISO 14001 ; ISO 45001 ; AQAP 2110 Quality Standards.
ARCUS Co. has adopted a policy toward the development and implementation of a company-wide quality assurance system which guarantees Research & Development and production practices in full compliance with the requirements of the Bulgarian State Standards, the international quality standard ISO 9001 ; ISO 14001 ; ISO 45001 ; AQAP 2110. The procedures and methods prescribed by these standardization systems foster the efforts invested by the company management and personnel in delivering to our customers a product up to the highest standards for quality, reliability, safety of function, ease of operation and customer satisfaction.
The management considers the quality assurance system implemented by the company as a process of its own, characterized by three major stages: input, processing and output:
1. The initial stage relates to the basic principles of the quality management system followed by ARCUS Co.:
-
- Focus on the client – the initial seller-buyer relations with our clients gradually evolve into partnerships.
- Personal commitment – the management of ARCUS Co. understand that commercial success may only be achieved and perpetuated through highly motivated and capable personnel.
- Long-standing partnerships with our suppliers – our suppliers guarantee that the input materials used in production meet all requirements in terms of quality and consistency.
- Continuous improvement – the highly qualified and experienced R&D team ensures the improvement of the existing products and is aimed at extending the line of products by engineering of new defence-related products to meet the contemporary requirements for improving the combat efficiency.
- Managerial decisions based on the system approach – the focus in the decision-making process is increased efficiency on all levels.
- Centralized organizational structure – the system of making and implementing decisions provides for effective control at each and every stage of production.
2. These principles are then processed in the second stage and implemented into the production activities of the company for the purposes of accomplishing the major objectives of the QA system employed by ARCUS Co.:
-
- Maximum satisfaction of the contracted and presumed requirements of our customers.
- Continuous improvement of the quality of the designed and produced items.
- Permitting no defects and claims as to the quality of our production.
- Effective approach toward the choice of suppliers.
- Preventive and corrective actions and their implementation through registering, processing and analyzing all inquiries, offers and claims.
- Creating and maintaining conditions that allow each staff member to contribute to achieving the goals of the Quality Management System.
3. The third stage relates to the output results of the quality assurance system: efficient production processes, high quality of the products offered and ultimately
-
- Fully satisfied requirements of our customers.
CORPORATE POLICY
FOR THE QUALITY, ENVIRONMENT, HEALTH AND SAFE LABOR CONDITIONS
- Application of methods for more effective management of human resources; involvement of all company personnel in active participation in quality management through training, motivation and consideration of possible risks.
- Maintaining open and constructive relationships and balancing the business interests of all stakeholders.
- Satisfying customer requirements with the application of new state-of-the-art technologies in order to improve quality and sustainable development in a dynamically changing market.
- Satisfying applicable statutory and other requirements as well as meeting compliance obligations and permitting regimes.
- Provide healthy and safe working conditions to prevent work-related injuries and illnesses, and to eliminate hazards and reduce risks to the WBR.
- Consult and involve workers and workers’ representatives, and support any quality and achievable initiative or good practice aimed at improving working conditions.
- Use of processes, technologies, materials, products, services and energy that reduce, control or avoid adverse impacts on the environment, including the prevention of pollution.
- Continuous improvement of the quality, environmental and WBR management system.
EXECUTIVE DIRECTOR:
M.Sc.,Eng., Trifon Trifonov